Super Alloys in Space Exploration
- Sylvia Rose
- Mar 5
- 3 min read
Updated: Mar 6
Super alloys have unique combinations of strength, corrosion resistance and high-temperature stability. Made primarily with nickel, cobalt and iron, super alloys are used in constructs enduring extreme environments.

From the searing heat of atmospheric reentry to the frigid vacuum of deep space, every component of a spacecraft faces extreme conditions. High-performance materials such as super alloys provide resilience and stability.
Nickel-based super alloys are most widely used due to superior resistance to oxidation and exceptional high-temperature stability. The addition of chromium can improve strength and resistance to oxidation by over 30%.
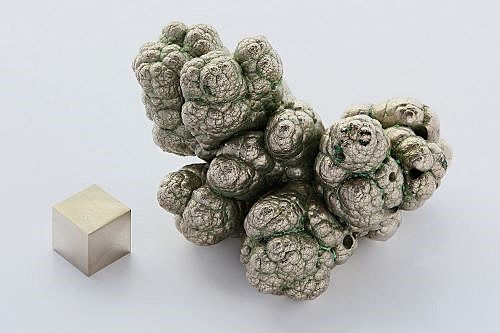
Cobalt-based super alloys are characterized by outstanding toughness and wear resistance. These alloys are particularly beneficial in environments prone to mechanical breakdown.
Iron-based super alloys, while less common in aerospace applications, are preferred for cost-effectiveness. They're strong, thus ideal for non-critical components where weight and budget constraints are priorities.
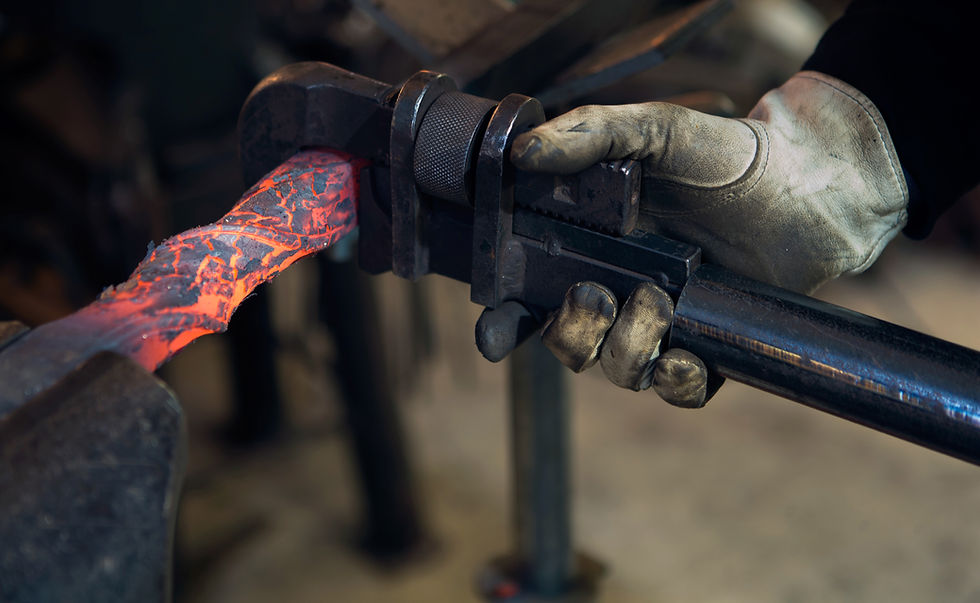
Qualities of Super Alloys
Exceptional Strength: At high temperatures, conventional metals lose strength and are prone to creep, or slow deformation under stress. Super alloys maintain strength even at temperatures over 1000°C (1832°F). This is desirable for components like turbine blades in rocket engines.
Corrosion Resistance: Hostile environments in space, whether the corrosive effects of rocket propellants or relentless radiation, create the need for materials to resist degradation. Super alloys resist oxidation, corrosion, and erosion for long-term reliability of spacecraft components.

Stability at High Temperatures: Spacecraft components are subject to drastic temperature fluctuations. In atmospheric reentry, the exterior of a spacecraft can heat up to several thousand degrees Celsius.
Super alloys retain structural integrity and dimensional stability at these temperatures, preventing catastrophic failures. Nickel-based super alloys, can withstand temperatures over 1200°C (2192°F).
Creep Resistance: The constant stress and high temperatures in rocket engines and other spacecraft systems can cause metals to deform over time, known as creep. Super alloys are designed to resist this phenomenon.

Super Alloys in Space Exploration
Rocket Engines: Extreme heat and pressure in rocket engines demand materials to withstand the conditions. Super alloys are used in combustion chambers, turbine blades, nozzles and other engine components. Nickel-based super alloys retain over 90% of original strength in high heat.
Spacecraft Structures: Super alloys are part of the structural integrity of spacecraft, especially in areas exposed to extreme temperatures or radiation. They're used in heat shields, which protect spacecraft during atmospheric reentry.
Super alloys are used in structural components including support frames and load-bearing elements. The strength-to-weight ratio of the alloys enables lighter designs.
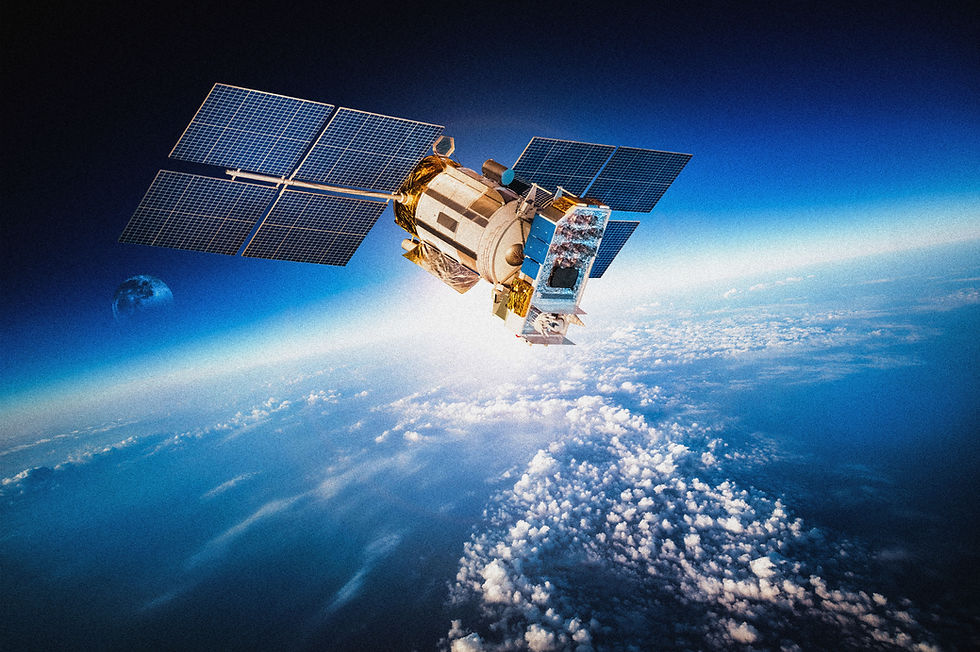
Gas Turbines: Power generation in spacecraft often relies on gas turbines, which require high-performance materials. Super alloys are used to manufacture turbine blades and other critical components.
Cryogenic Systems: Some spacecraft components, such as fuel tanks, require materials to function at very low temperatures. Many super alloys maintain strength and ductility at cryogenic temperatures.
Advanced Manufacturing: Super alloys can be used in advanced manufacturing processes like 3D printing to create complex and customized parts for spacecraft.

Non-Fiction Books:
Fiction Books:
READ: Lora Ley Adventures - Germanic Mythology Fiction Series
READ: Reiker For Hire - Victorian Detective Murder Mysteries