What Robots Need to Function & Survive
- Sylvia Rose
- Mar 3
- 4 min read
Robots are automations in all shapes and sizes, yet they need key factors to function and survive. These include power or energy, accurate senses, an efficient brain able to make decisions, and matching accessories.

Power: The Spark of Life
The basic requirement for any robot is a reliable power source. The optimal power source depends on the robot's size, complexity, and intended use.
Electricity
Stationary robots, such as industrial arms used in assembly lines, rely on direct electric power. This ensures an uninterrupted power supply, keeping the bots always ready for action. However, its mobility is limited.
Batteries
Mobile robots enjoy freedom of movement but depend on of charge cycles and battery life. Rechargeable lithium-ion and lithium-polymer batteries are often used. They're lightweight with strong energy density.
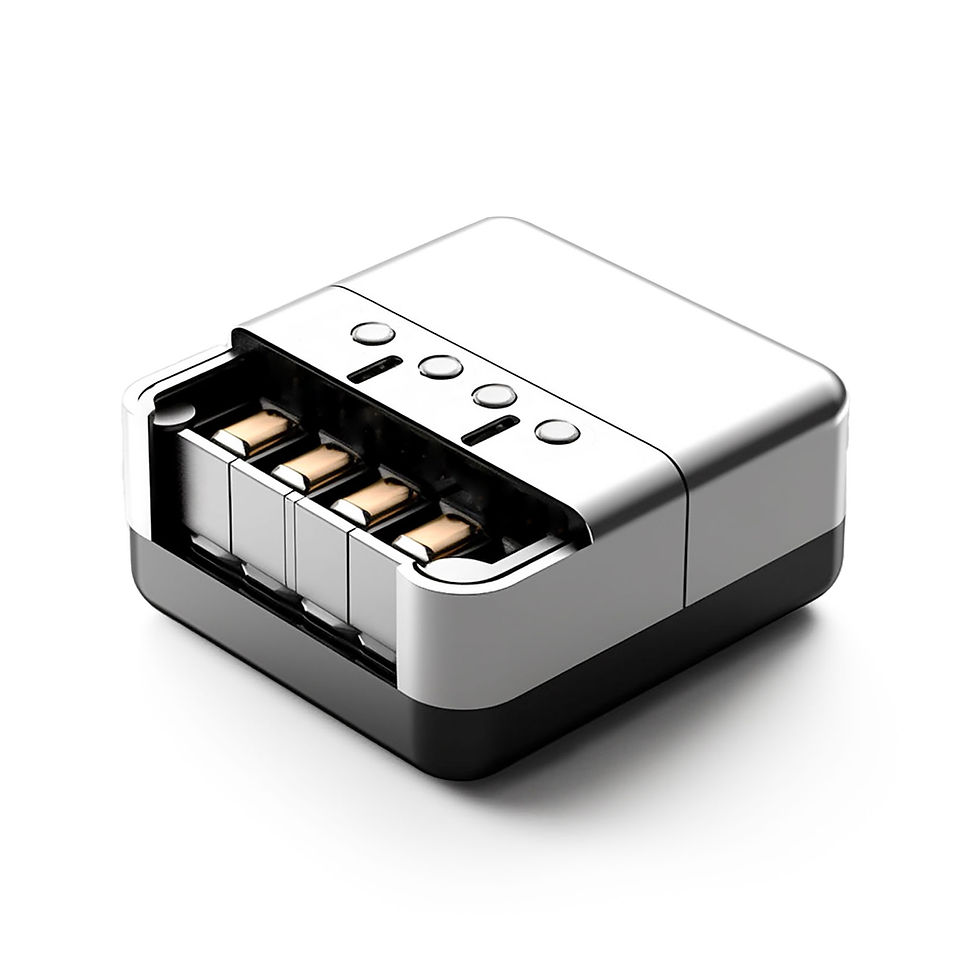
An average lithium-ion battery can store about 150-200 watt-hours per kilogram. This is ideal for consumer electronics. Efficiency varies. Battery life ranges from 2 to 5 years depending on usage.
Hydraulics/Pneumatics
This system is used for heavy-duty work like construction or manufacturing. Hydraulic robot arms operate using pressurized hydraulic fluid. The fluid supplies the force for the arm to lift, move, and handle heavy loads with precision.
Solar power
Robots like the Solar-Powered Autonomous Rover use solar panels to convert sunlight into electricity. The robots can operate 24 hours a day in areas with high sunlight. Weather conditions and location are considerations.

Sensory Input: Perceiving the World
A robot's ability to understand and interact with its environment depends on its sensory perception. A suite of sensors create the robot's eyes, ears, and skin.
Ultrasonic sensors can measure distances up to 4 meters, while LIDAR can create detailed maps of environments with millimeter accuracy. These sensors are used for navigation, obstacle detection, and decision-making.
Vision Systems: Cameras and image processing software enable robots to identify objects, navigate obstacles, and recognize faces.
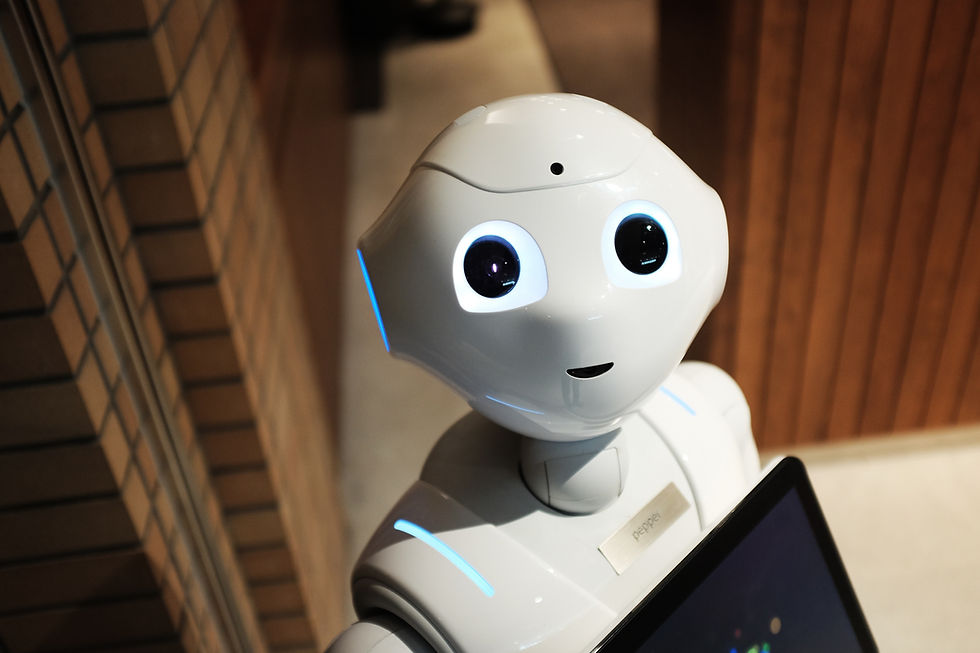
Proximity Sensors: Infrared, ultrasonic, and lidar sensors help robots detect nearby objects and avoid collisions.
Force and Torque Sensors: These enable robots to feel the pressure they apply to objects, crucial for delicate tasks like assembling electronics or performing surgery.
Environmental Sensors: Measuring temperature, humidity, and other environmental factors allows robots to adapt to changing conditions and perform tasks like monitoring air quality.
Choosing the right sensors affects robot performance. Top-tier sensors, like 3D cameras, enhance capabilities but come with higher costs.
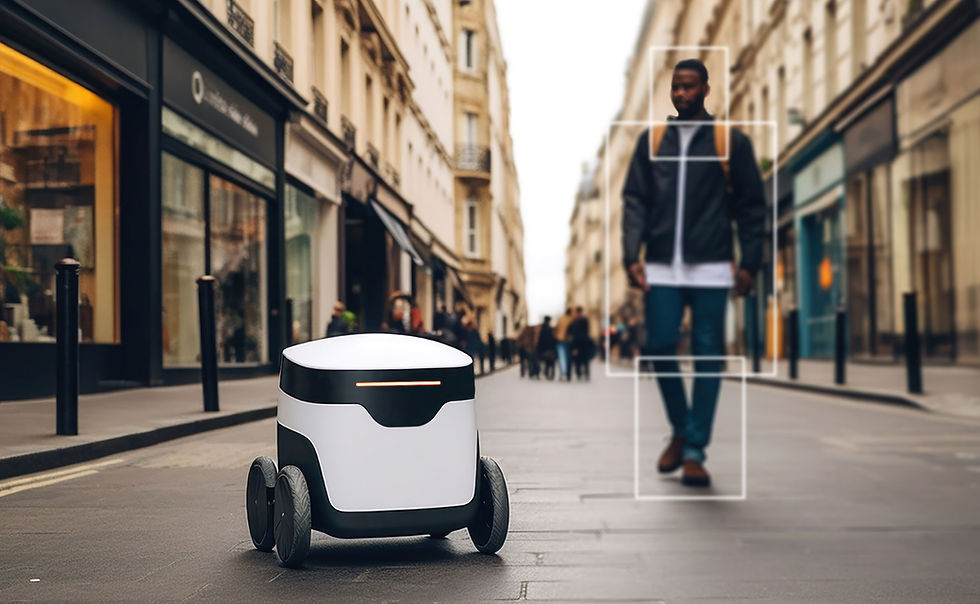
Processing: the Brain
Control systems are the brains of the robot. They process data collected from sensors and translate it into actions. Advanced robots often use machine learning algorithms to improve adaptability and decision-making.
Some, like warehouse robots, can be programmed to refine their paths continuously to avoid obstacles.
Central Processing Unit (CPU): This is the central hub for executing code, controlling movements, and managing sensor data.

Graphics Processing Unit (GPU): Increasingly important for robots relying on complex vision systems or simulations.
Embedded Systems: Specialized processors designed for real-time control and efficient power consumption.
Artificial Intelligence (AI) and Machine Learning (ML): Algorithms that allow robots to learn from experience, adapt to new situations, and make autonomous decisions.
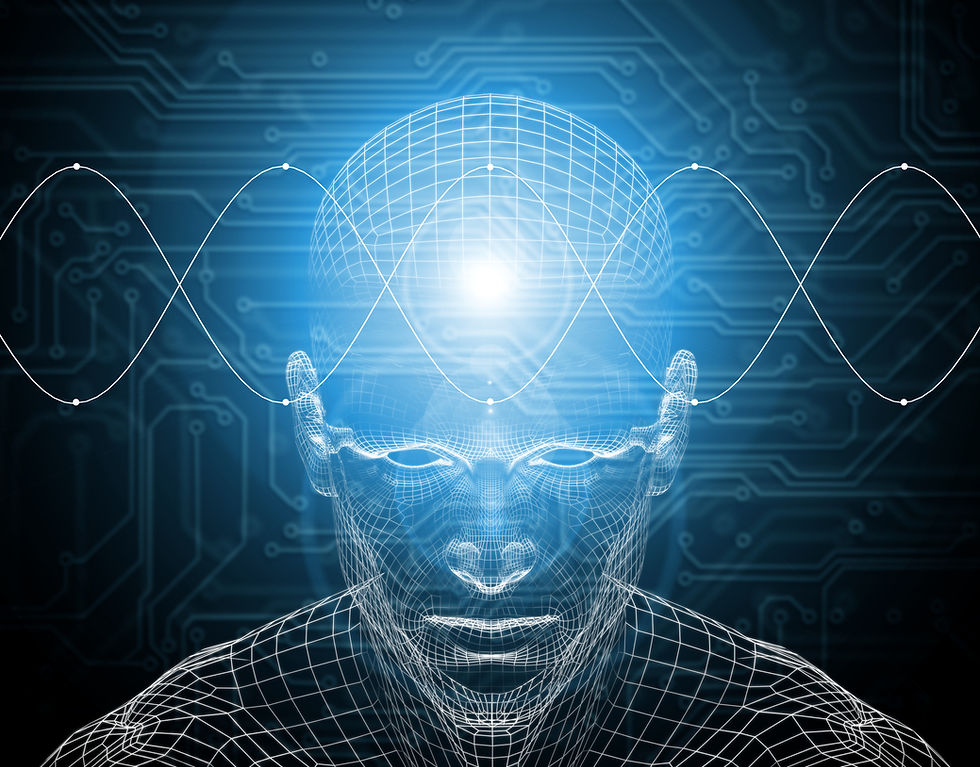
Actuation and Mobility: Taking Action
Once a robot has processed information and made a decision, it translates the decision into physical action. It needs actuators and mechanisms for movement.
Actuators are the driving force behind a robot’s movement, transforming energy into physical actions. They can be electric, hydraulic, or pneumatic.
Each type has its advantages. Electric actuators are efficient for precise tasks, while hydraulic ones can handle larger loads.

Motors: power wheels, arms, and other moving parts.
Servomotors: precise control over position and speed, as in complex movements and fine manipulation.
Hydraulic and Pneumatic Actuators: high force and speed for heavy-duty applications.
Locomotion Systems: wheels, tracks, legs, or even wings, depending on robot's intended environment and task.
The choice of actuator affects robot strength, speed, and precision. For example, automation in packaging often uses electric actuators for efficiency and smooth movement.

Software and Programming: A Purpose in Life
Programming provides robots with instructions, defining their behavior and capabilities.
Robot Operating System (ROS): A widely used framework for developing robotic software, providing tools and libraries for tasks like perception, motion planning, and control.
Programming Languages: Python, C++, and Java are common choices for writing robot code.
Simulation Environments: Software that allows developers to test and refine robot programs in a virtual environment before deploying them in the real world.
Networking & Interaction with Others
Many robots depend on network connectivity for data exchange and overall control. CoBot, a collaboration robot, can work with multiple other robots to manage assembly tasks. Reliance on connectivity has drawbacks, such as vulnerability to cyber threats.

Non-Fiction Books:
Fiction Books:
READ: Lora Ley Adventures - Germanic Mythology Fiction Series
READ: Reiker For Hire - Victorian Detective Murder Mysteries