Robot Lubrication: Grease the Machine
- Sylvia Rose
- Mar 11
- 5 min read
Lubrication is integral to keep mechanical parts moving smoothly. Robot lube increases performance and lifespan. From mineral oils to smart lubricants, here are the basics of robot grease today.

Robot lubrication production is a niche industry. Fast growing, it's characterized by specialized formulations, advanced manufacturing processes, and discerning procurement strategies.
Robot Lubrication Needs
Robot operating environments can range from sterile cleanrooms to extreme industrial settings. Lubricants need to withstand temperature fluctuations, resist contamination and prevent build-up of static electricity.
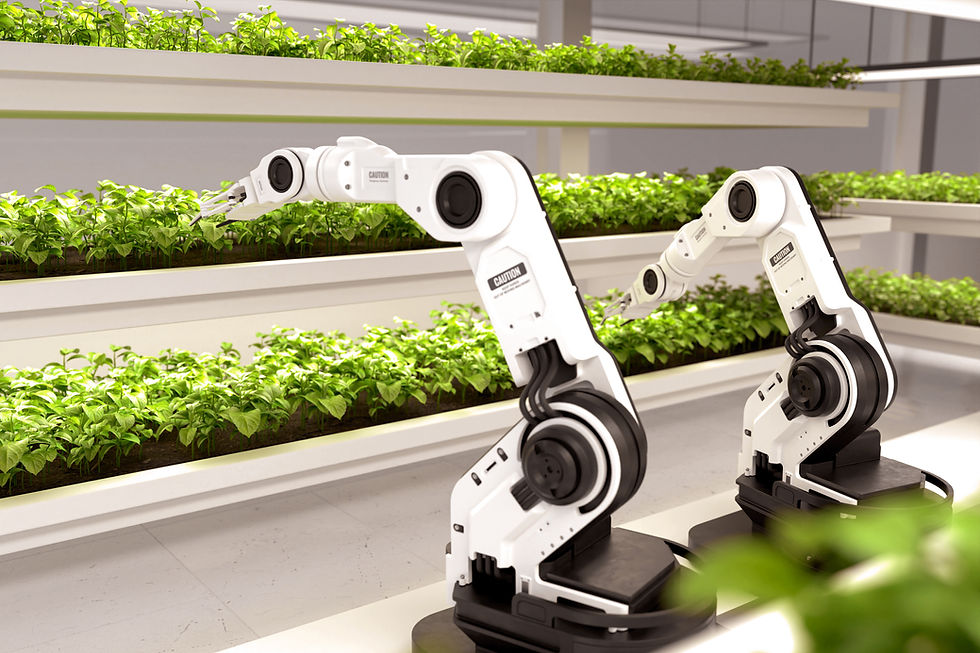
Robot lube is used for:
Friction Reduction: Minimizes energy loss and extends the lifespan of components like gears, bearings, and joints.
Wear Protection: Prevents premature component failure due to contact and abrasion, saving money and time.
Heat Dissipation: Cools down moving parts, preventing overheating and maintaining dimensional stability. Less friction means lower temperatures, which keeps components from overheating.
Corrosion Protection: Shields against environmental factors that can degrade metallic components.
Noise Reduction: Dampens vibrations, contributing to quieter operation.
Sealing: Provides a barrier against contaminants like dust, moisture, and chemicals.

Lubricant Types
Greases are semi-solid lubricants. They provide long-lasting performance, especially under high pressure and are favored for motors, gears, and bearings.
Lithium-Based Grease
These are versatile, all-purpose water resistant greases with high-temperature performance. They're widely used in gearboxes, bearings, and other general lubrication applications. Molybdenum disulfide-enhanced lithium grease is preferred for heavy-duty joints.
Lithium based greases suit automotive and industrial robots. In manufacturing plants lithium grease adds to robot longevity and endures high temperatures.
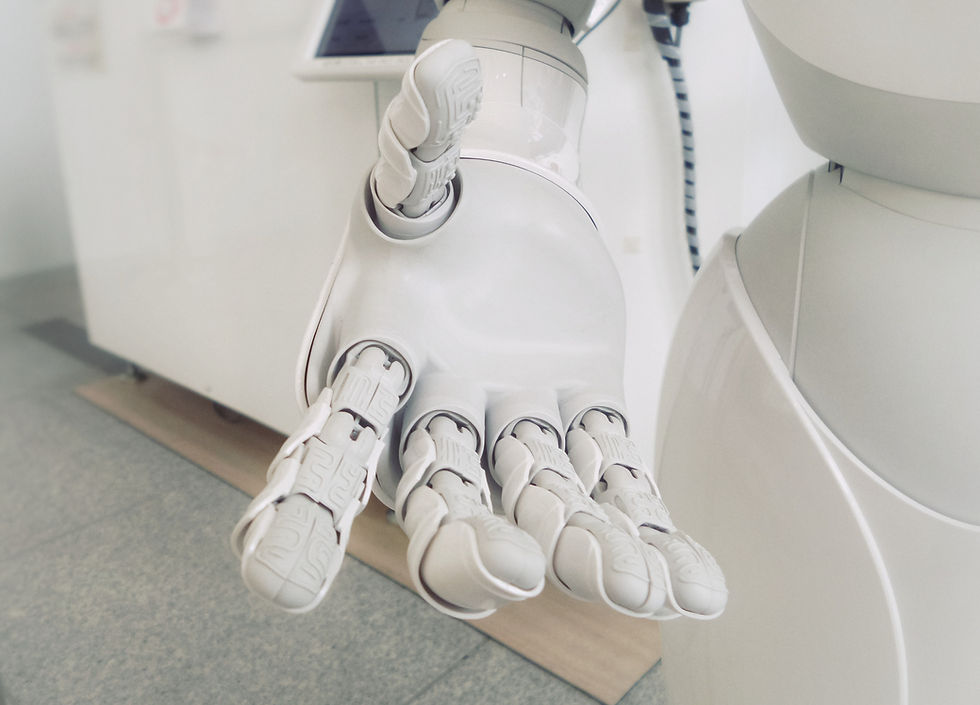
Mineral Oil
Though widely used, mineral oils may not reach the advanced performance levels of synthetic oils. Mineral oils are suited for everyday robotics tasks. Pure mineral oil is nontoxic.
However, industrial grade mineral oil has dangers. Overexposure can lead to breathing problems, skin irritation and types of cancer.
Synthetic Oils
These oils outshine traditional options because they are engineered for better performance. They can decrease friction by about 30 percent compared to standard mineral oils.
Surgical robots require precision and cleanliness. Synthetic oils help prevent contamination while increasing smooth performance.

Synthetic Grease
Formulated from synthetic oils like PAO (Polyalphaolefin) or ester oils, these greases have superior performance in extreme temperatures and high-speed applications.
They have strong oxidation stability and resist degradation. PAO-based grease for instance is used for robotic arm joints needing high precision.
Silicone Grease
Silicone-based greases have excellent water resistance, a wide temperature range, and are compatible with plastics and elastomers. They're used in applications needing electrical insulation or contact with sensitive materials.
Excellent for high-precision components, silicone greases can handle both extreme temperatures and moisture. They lubricate medical robots, ensuring cleanliness and functionality.
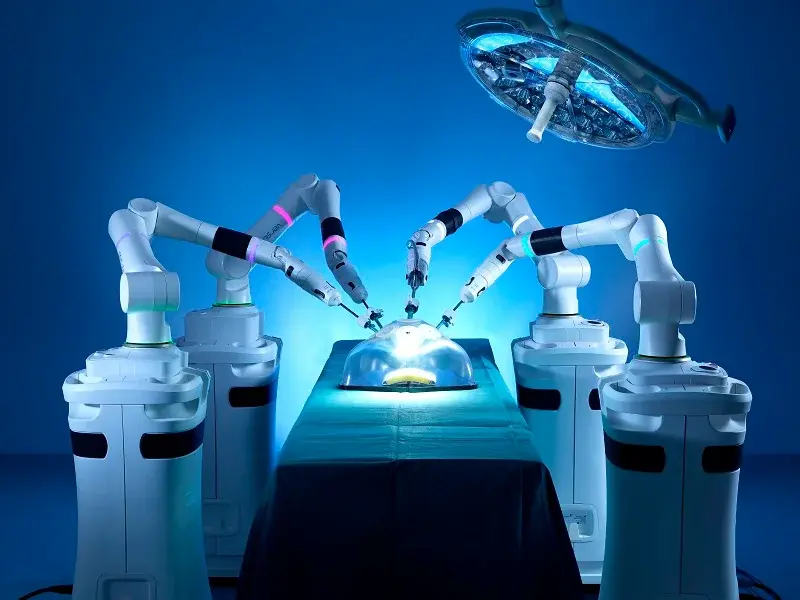
Fluorinated Grease (PFPE/PTFE)
These greases offer exceptional chemical resistance, high-temperature stability, and low friction coefficients. They are ideal for robots operating in harsh or corrosive environments.
They tend to be more expensive but offer superior protection where needed. PFPE grease for example is used for robots in chemical processing plants.
Dry Film Lubricants
These lubes, such as graphite, molybdenum disulfide or PTFE coatings, are applied as a thin film and provide lubrication without oils or greases. They're used when cleanliness is critical or where liquid lubricants are not practical.
PTFE coat the screw threads of miniature robots. Dry lubricants are effective in extreme temperatures, remaining stable up to 300°C.

Smart Lubricants
These have sensors to monitor lubricant condition in real-time, enabling predictive maintenance to prevent stalls and downtime. In autonomous vehicles, robots implement advanced lubrication systems to reduce friction in actuators and rotating parts.
Bio-based Lubricants
Interest rises in bio-based robot lubricants, seeking environmentally friendly and sustainable options. Eco technologies promote the use of bio-lubricants from renewable resources like vegetable oils.
Manufacture & Composition
Production of robot grease combines base oils, thickeners, and additives.
Base Oils: These provide the primary lubricating properties. Mineral oils, synthetic oils (PAOs, esters), and silicone oils are commonly used. Some synthetic oils are effective between -50°C to 200°C.

Thickeners: They determine the grease's consistency and prevent the oil from leaking out. Common thickeners include lithium soaps, calcium soaps, polyurea and clay.
Additives
Extreme Pressure (EP) Additives: Enhance load-carrying capacity
Anti-Wear Additives: Reduce friction and wear
Corrosion Inhibitors: Prevent rust and corrosion
Oxidation Inhibitors: Extend lubricant life
Friction Modifiers: Fine-tune friction characteristics
Dyes: Dyes can assist in the identification of lubricants
The manufacturing process typically involves mixing the base oil, thickener, and additives under controlled conditions of temperature and pressure. The mixture is then homogenized and refined to achieve the desired consistency and properties.

Grease Production
Selecting Base Oil: The process starts with choosing the right oil based on viscosity and thermal properties.
Adding Thickening Agent: Ingredients such as lithium soap are added to create a gel-like consistency.
Homogenization: Everything is mixed under controlled conditions to achieve uniformity.
Quality Control: The final product undergoes rigorous testing for performance and stability before distribution.
Oil Production
Oil manufacturing refines crude oil through certain steps.
Distillation: Crude oil is heated and separated by boiling points, converting each fraction into usable oil.
Hydrocracking: This process removes impurities, enhancing stability, which can improve performance by as much as 20 percent.
Adding Performance Improvers: Various additives are mixed in to boost characteristics like anti-wear properties.
Motor oil, brake fluid or other low-viscosity oil can be used for some robots.
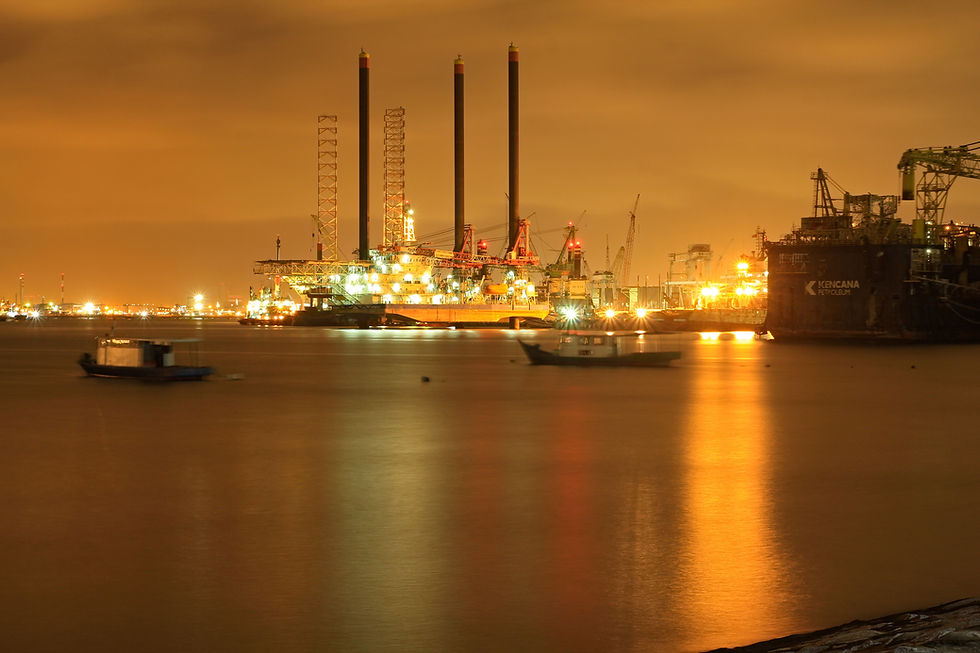
Dry Lubricants
Dry lubricants are made by grinding raw materials like graphite into fine powders with smooth slippery qualities. The powder may be combined with a binder to improve adherence to surfaces during application.
Procuring Robot Lubricants
Lubricant Manufacturers: Companies specializing in production of industrial and specialty lubricants include Shell, Mobil, Kluber Lubrication and Nye Lubricants.
Robot OEMs (Original Equipment Manufacturers): Robot manufacturers offer their own branded lubricants or recommend specific lubes for their robots.
Distributors: These companies distribute lubricants from various manufacturers. Choosing the right lubricant and supplier ensures long-term performance and reliability of robotic systems.

READ: Lora Ley Adventures - Germanic Mythology Fiction Series
READ: Reiker For Hire - Victorian Detective Murder Mysteries