How to Make Iron Oxide Pigment at Home
- Sylvia Rose
- Sep 1, 2024
- 5 min read
Updated: Nov 3, 2024
Make non-toxic iron oxide pigments for painting, dyes, glazes, artistic to industrial uses. Iron oxide (Fe2O3) or rust exists on Earth from times of creation. Experimentation can yield various textures and colors. This is a straightforward project for DIY enthusiasts and rustic artisans.

What Are Iron Oxide Pigments?
Iron oxide pigments of rust are compounds made from iron and oxygen. They can manifest in various colors, typically red, yellow, brown and black, valued for opacity and UV stability. While synthetic pigments fade over time, natural iron oxide pigments last longer.
Iron oxides are natural, inexpensive and durable pigments in paints, coatings, glazes and colored concrete. Colors commonly extracted are earthy yellow, orange, shades of red, brown, black range.

Materials Needed
Iron Source: You can use iron filings, rusted iron, or iron sulfate. For a more authentic pigment, rust is preferred.
Water: To facilitate the extraction process.
Vessel: A non-reactive container for mixing (glass or ceramic works best).
Filter: A fine sieve or coffee filter to separate solids from liquids.
Heat Source: A stovetop or hot plate.
Solvent: If you want to create a more concentrated pigment, you may need a solvent like vinegar (acetic acid).
Mortar and Pestle: For grinding the pigment once it’s dried.
Safety Gear: Gloves, goggles, and a mask to protect against dust and fumes.

Step-by-Step Guide to Making Iron Oxide Pigment
Step 1: Prepare the Iron Source
Begin with an iron source. If collecting rust by scraping it from rusty objects, ensure it’s clean and free from contaminants. To create rust simply expose iron or steel to moisture and oxygen.
Iron oxides are chemical compounds composed of iron and oxygen. Several iron oxides are recognized. Ferric oxyhydroxides are a related group of compounds, rust being one of the most well-known examples.

To start the iron oxide pigment experiment use nails, steel wool, things found around the house. Experiment with different substances, as not all rust is created equal. A number of colors can be coaxed from iron oxide compounds.
Choose metal (iron or steel) that rusts. Some metal materials won't rust, including:
Aluminum. An abundant and versatile metal, aluminum containing no iron, except in some alloys. Aluminum corrodes, but doesn't rust.
Copper, a native metal, meaning it can be found in nature in its pure metallic form
Brass, a zinc-copper alloy
Bronze, a tin-copper alloy
Galvanized steel
Stainless steel
Tin
Chrome (Chromium)
Gold & Silver

Rust can develop on any metal containing iron, such as steel, iron, and cast iron. The speed at which rust appears on metal surfaces is influenced by humidity levels, presence of oxygen and the type of metal.
Leave the iron in a humid environment or water bath. Rust forms. Creation can take many days. Process is accelerated by adding a solvent such as hydrogen peroxide or vinegar. Don't mix these two. Salt, as in brine, is also a potent rust accelerator.

Step 2: Extract Pigment
Place your iron source in a non-reactive container and add enough water to cover it. Non-reactive containers include stainless steel, ceramic, glass and enamel coated cookware. Reactive materials include aluminum, cast iron and copper.
If using iron filings or iron sulfate, grind the iron finely. Let the mixture sit several hours to allow the iron oxide to dissipate into the water. Stir occasionally with non-metallic rod, stick, spoon or other stirring device to help the process.

Step 3: Filter the Mixture
After letting the mixture sit, it’s time to filter out the excess material. Use a fine sieve or cheesecloth to separate the liquid and precipitate from the solid iron bits. The liquid should be dark and rich in iron oxide.
Step 4: Precipitate the Pigment
Transfer the filtered liquid into a saucepan and heat it gently on the stovetop. As the water evaporates, the iron oxide will begin to precipitate from the solution. Keep a gentle simmer and don't let it boil.

Step 5: Dry the Pigment
Once most of the water has evaporated and a thick sludge forms, remove the saucepan from heat. Let it cool a few minutes. Transfer the iron oxide paste onto a flat surface on parchment paper or in a glass container, to dry completely. An oven at low temperature (around 200°F or 93°C) can speed up the drying process.
Step 6: Grind into Powder Pigment
Once iron oxide is dry, use a mortar and pestle to grind it into a fine powder. The finer the powder, the smoother and more vibrant the pigment will be. Store pigment in an airtight container away from moisture.

Tips for Success
Experiment with Color: Different iron sources may yield different shades. For instance, varying the oxidation state can create darker or lighter pigments.
Safety First: Always wear safety gear when working with powdered substances. Iron oxide dust can be harmful if inhaled.
Keep It Natural: Avoid using synthetic additives or solvents if the pigment is to be as eco-friendly as possible.
Test Pigment: Before using it for larger projects, test pigment on a small canvas or paper to see the final color and how it behaves with the medium.
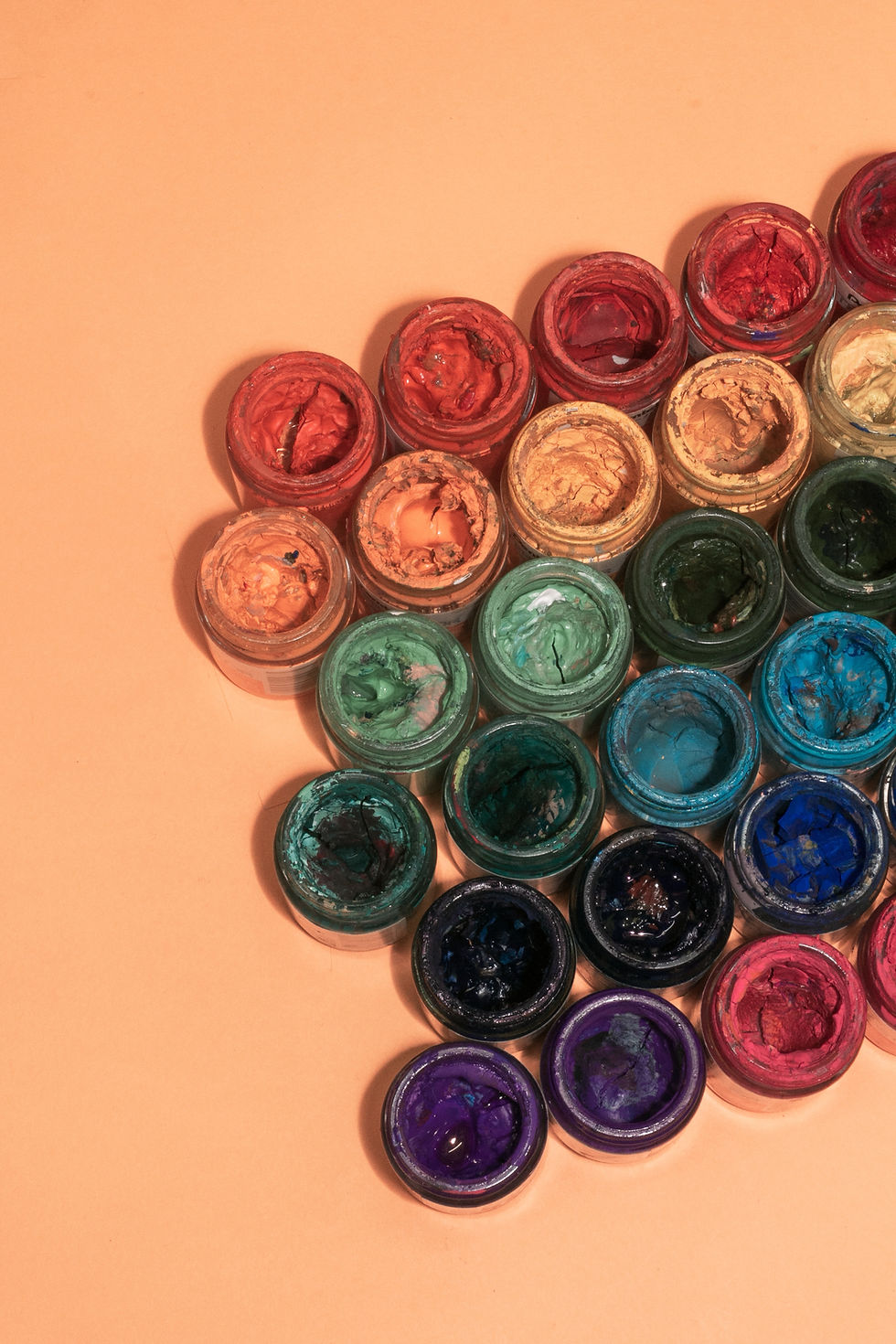
Green rust is a corrosion crust on iron and steel surfaces. It occurs in nature as the mineral fougèrite. Fougèrite is unstable in air, changing color at normal conditions. Any elements containing zinc retain their green color and transparency. Zinc itself is one of the "unrustibles".
The green (or green-black, blackish), hexagonal, transparent platelets transform quickly into yellow-brown to brown, opaque, often poorly crystalline, brittle iron oxyhydroxides (limonite, goethite, lepidocrocite). Known previously as "Green Rust", it's mainly from iron-rich slags.

Making iron oxide pigment is a rewarding and straightforward process. It allows for creativity with organic materials.
Non-Fiction Books:
Fiction Books:
READ: Lora Ley Adventures - Germanic Mythology Fiction Series
READ: Reiker For Hire - Victorian Detective Murder Mysteries