Smelting Metals: Metalwork & Alchemy
- Sylvia Rose
- Aug 20, 2024
- 4 min read
In alchemy an essential piece of equipment is the hearth or forge. Smelting metal applies heat and a reducing agent to separate one or more metals from ores or impurities. Known as extractive metallurgy, this process releases metals like iron, copper, silver, tin, lead, and zinc.
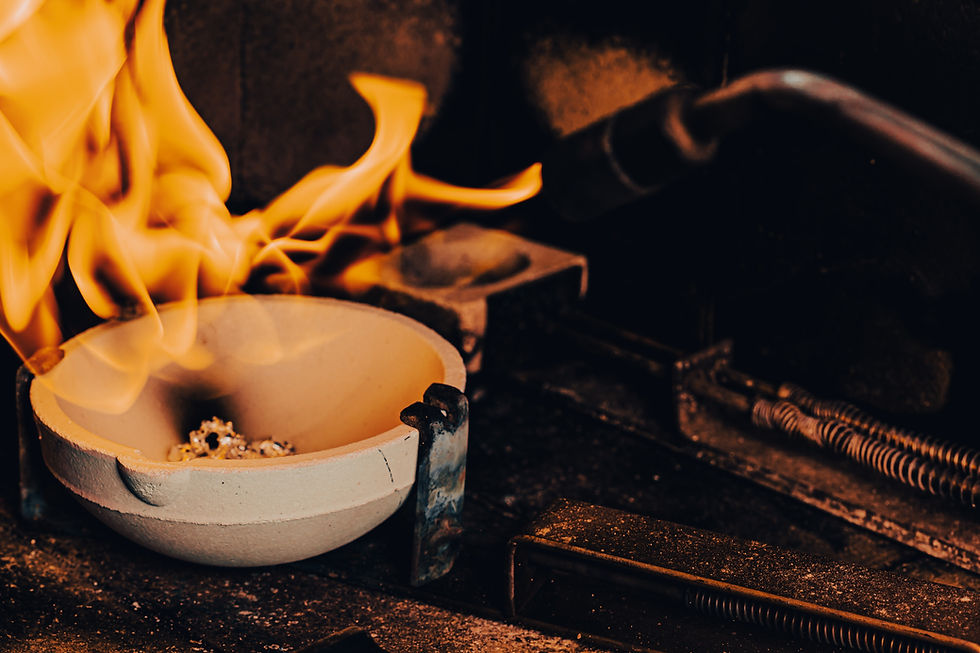
While smelting can be melting, not all melting is smelting. Metals are pivotal elements in alchemy and heat is essential for many alchemical processes. The forge is a hearth used for heating metals. The smith needs to raise metal to a temperature for shaping.
Copper and iron are two of the metals of antiquity. These are the metals found in raw form, easily accessible at ground level. They can be shaped with hand tools like stone hammers. Both copper and iron are also found in ores and smelted to release them from the ore.

Of these, copper is one of the major metals or alchemy, while iron is a major metal of building and mass production. Iron is said to protect against evil magic. Copper is used in alchemy recipes for creation of "gold" and "silver", as well as the all-important asem.
Prior to mining, iron comes almost exclusively from meteorites. It's soft enough to be shaped with stone tools. In alchemy metals have a quintessence or life force. Metals like iron and lead in the ground are thought to be immature versions of precious metals like silver and gold.
Copper can form in sulfur ores or oxide ores. Oxide ores produce a high-grade copper. Oxides can often be dissolved in weak acid, making copper recovery efficient. They include malachite Cu₂CO₃(OH)₂, azurite, chrysocolla and cuprite. Sulfides need a different process.
Sulfide ores are roasted to release copper (Cu), zinc (Zn), or lead (Pb) in concentrate which needs more processing. Sulfide ores include chalcopyrite (CuFeS2), the most abundant copper source; and covellite (CuS). Iron ores include hematite (Fe2O3) and magnetite (Fe3O4).

Smelting of ores signifies a pivotal moment in the history of mankind. Although the production of copper and bronze was important, the development of iron metallurgy rapidly transforms into an industrialized procedure.
In smelting, heat and a reducing agent break down ore. This releases elements such as as gases, slag or dross, while metal remains. The reducing agent is a carbon-based fossil fuel, historically charcoal.

Roasting converts the sulfides into oxides, such as the black powder copper II oxide, more easily reduced to the metal. Heating the ore in the presence of natural oxygen from the air causes the ore to oxidize and release sulfur as sulfur dioxide gas.
Copper II oxide is created fby heating copper in air at around 300 – 800 °C (572 - 1472 °F): 2 Cu + O 2 → 2 CuO. This can be done in an ordinary fire.

Orange flames range from around 1100 °C to 1200 °C (2012 °F to 2192 °F)
White flames are hotter, measuring 1300 °C to 1500 °C (2372 °F to 2732 °F). The brighter white, the higher the temperature.
Blue flames, or flames with a blue base, are up to twice that hot, with temperature approximately 2500°C to 3000°C (4532 °F to 5432 °F)
Violet flames burn hotter than 3000 °C (5432 °F)

Thus roasting removes carbon or sulfur from carbonates and sulfides, allowing direct oxide reduction in an oxidizing environment. Oxidation happens when an element combines with oxygen (0) to give an oxide. For example, the oxide of hydrogen (H) is water (H20).
Below, the copper II oxide is turning reddish as the narrow part of the pipette collects evaporated recondensed water.

Iron rises to prominence only after development of furnaces and refinement of the technique for "hardening" metal at high temperatures. The advancements in metallurgy of terrestrial iron soon make it suitable for everyday use.
Industrial-scale production of steel goes back to the Near East c.1800 BCE. Between 1200 and 1000 BCE iron is heavily mined in the mountains of Armenia and processed through smelting.

Non-Fiction Books:
Fiction Books:
READ: Lora Ley Adventures - Germanic Mythology Fiction Series
READ: Reiker For Hire - Victorian Detective Murder Mysteries