Pyrometallurgy: Ancient Processes of Modern Alchemy
- Sylvia Rose
- Nov 13, 2024
- 6 min read
Pyrometallurgy is the high-temperature processing of ores to extract and refine metals. It uses alchemical processes in a modern industrial setting. The four main steps of pyrometallurgy are calcination, roasting, smelting and refining or purification. Here's a quick look at each.

Essentially, pyrometallurgy acts as a transformation pathway turning raw minerals into usable metallic products. By applying heat, pyrometallurgy seeks to extract and purify metals from both ores and concentrates. These metal processing steps are basics in ancient alchemy.
The specific processes may vary depending on materials involved and metals recovered. In alchemy, practitioners are proficient in all four steps as well as alloying and amalgamating, assaying, gilding, distillation, sublimation, painting, glazing, metal plating and more.
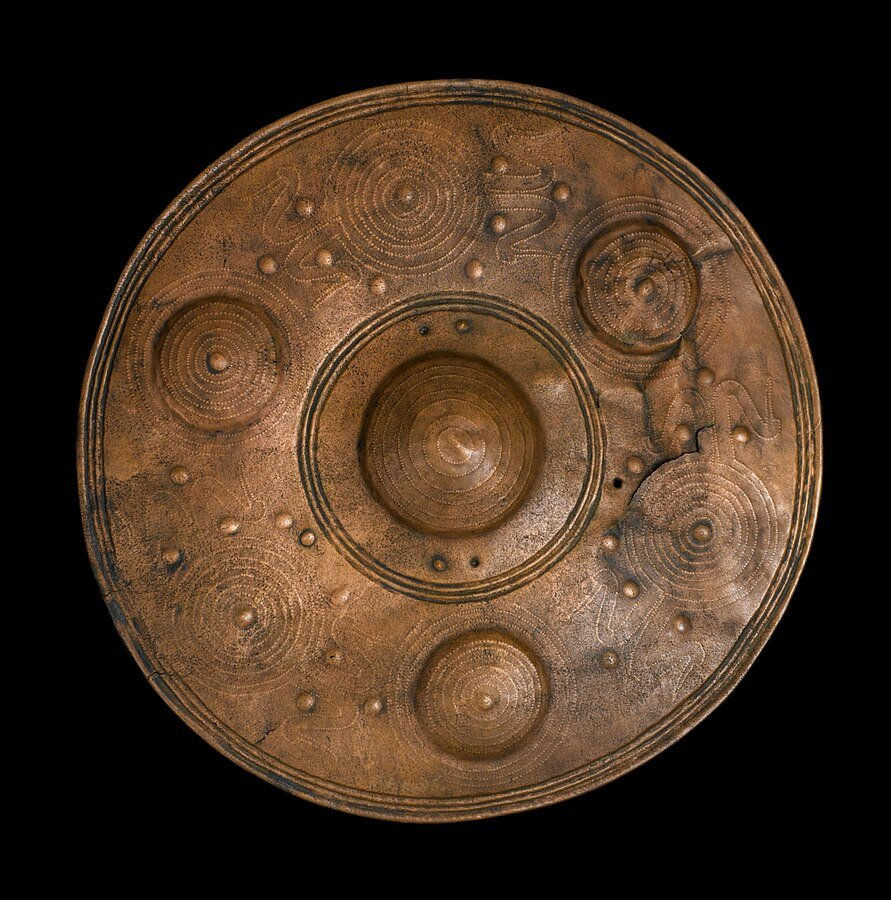
Alchemy begins in practice with Maria Prophetissa or Mary the Jewess in Alexandria c. 100 AD. She works with metals and alloys, speaking in a language unfamiliar to modern ears, which is later considered mystic.
For instance in early metallurgy and alchemy, copper is called Venus and iron Mars. It appears so in the Leyden Papyri of c. 250 AD. This concept is further developed and sticks throughout the Middle Ages, takes on an enigmatic factor echoed in the arts, literature, laws and money scams of medieval Europe.
While the so-called mystic element develops a large following, the practical alchemy Mary actually teaches is invaluable to the ancients. It's still used today.
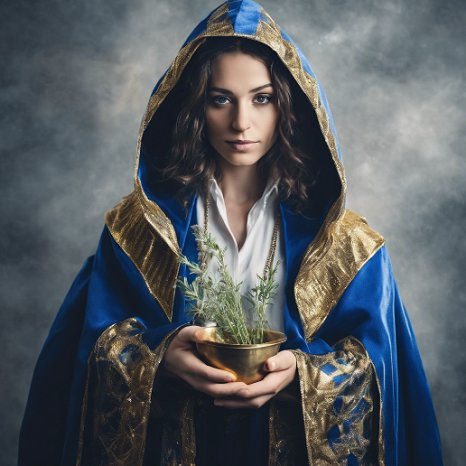
Step 1: Calcining (Calcination)
Calcining is the first step in the pyrometallurgical process, which involves the heating of ores at high temperatures but below their melting points. This process is meant to drive off volatile substances and remove moisture, carbon dioxide, and other gases from the material.
Calcining marks the initial stage of pyrometallurgy. Its main goal is to remove volatile compounds from the ore, such as water and carbon dioxide. This often involves heating ores to temperatures below their melting point, facilitating the breakdown of minerals.

Transformations:
During calcination, carbonates and hydroxides are converted to oxides. For instance, when limestone (calcium carbonate CaCO₃) is heated, it decomposes into lime (calcium oxide CaO) and carbon dioxide (CO₂).
This process is vital in metallurgical operations, particularly iron and steel production. The transformation not only prepares the material for the next processing stages but also refines it by reducing impurities.

Practical Example: Limestone Calcining
In the cement industry, calcination is vital for producing quicklime, which is a key ingredient in cement. For instance, the calcination of 1 ton of limestone can yield approximately 0.56 tons of quicklime and release about 0.44 tons of CO₂. This shows how critical the calcining process is for both material preparation and environmental impact.
Step 2: Roasting
Following calcining, the process of roasting involves heating the ore in the presence of air or oxygen at elevated temperatures. This step primarily aims to alter the chemical composition of the ore, often facilitating the extraction of metals.
Roasting may be used with sulfidic ores in the presence of oxygen. This process is important to convert metal sulfides into metal oxides, which can be more easily reduced in later stages. Roasting is one of the essential skills of ancient alchemists.
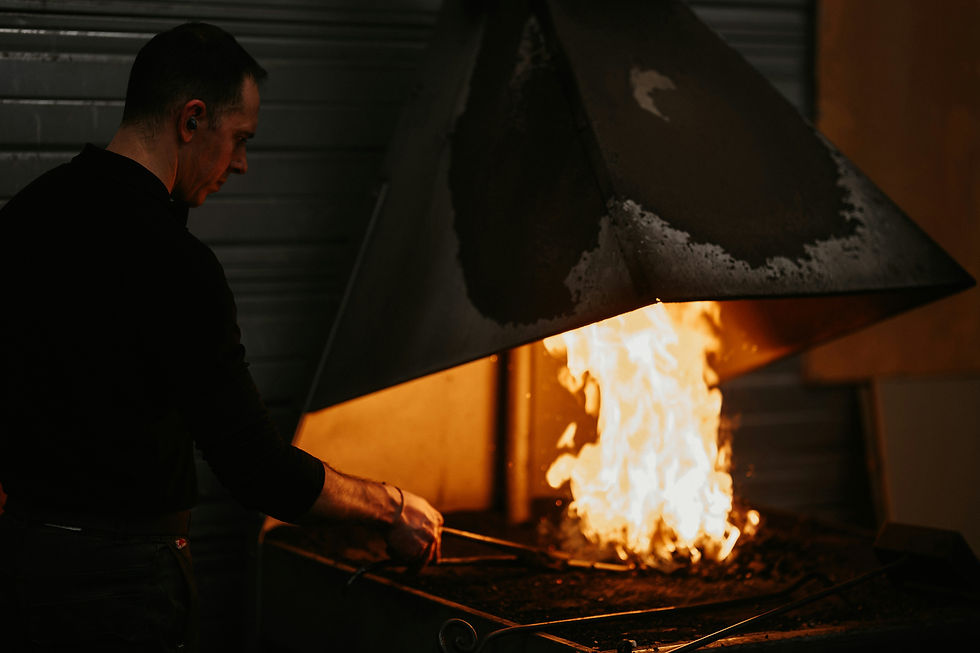
Transformations:
Roasting is particularly effective in converting sulfide minerals into oxides. For example, roasting copper(I) sulfide (chalcopyrite) results in the formation of copper oxide and sulfur dioxide, essential for further processing. This transformation allows for the subsequent steps to yield elemental copper.
Roasting integrates oxidation and thermochemical reactions. For example, if copper(I) sulfide (Cu₂S) is roasted, it transforms to compounds known today as copper(II) oxide (CuO) and sulfur dioxide (SO₂). This transformation is crucial for efficiency of the subsequent smelting process.
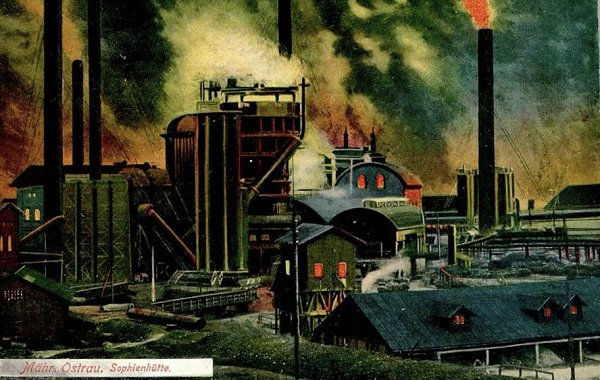
Practical Example: Copper Roasting
Commonly, sulfide ores like chalcopyrite (CuFeS₂) are roasted in the copper industry to reduce sulfur and convert the ore into a more manageable oxide form. This process can improve metal concentration by up to 90%, making it more suitable for the following smelting phase.
Step 3: Smelting
Smelting follows the roasting process and is characterized by the melting of the ore or concentrate to separate metallic elements from the non-metallic residues. It typically involves the use of a flux to combine with the gangue, facilitating the formation of a liquid slag.
Following roasting, smelting is where the real extraction occurs. This process uses intense heat and a reducing agent, typically carbon in the form of coke, to separate metals from their ores.

In this step, heat induces the reduction of metal ores. For instance, during the smelting of iron ore (Fe₂O₃), carbon reduces the ore, yielding iron and carbon monoxide. Here, the carbon monoxide produced can be used in other processes, making this phase efficient and interconnected.
Practical Example: Iron Smelting
The historical significance of iron smelting cannot be overstated; it has been a cornerstone of civilization. In a modern blast furnace, approximately 1.5 tons of iron can be produced from 2.5 tons of iron ore, highlighting the productivity of smelting processes that have evolved over time. This molten iron can then be cast into various shapes or used to produce steel.

Transformations:
During smelting, metal oxides are reduced to pure metals. For example, in the production of iron from iron oxide, a carbon source (often coke) is used in the blast furnace, reducing iron(III) oxide to produce molten iron.
Here, iron is extracted from its ore, while carbon monoxide gas is produced, which can also be used in further metallurgical processes.
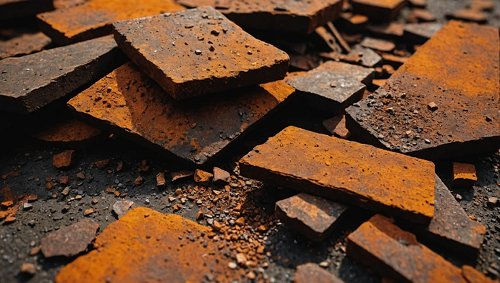
Step 4: Refinement or Purification
The refining process is the final step in the pyrometallurgical approach, where impurities are removed from the crude metal to produce a purer form suitable for commercial use. This step is a series of heating and cooling cycles with addition of specific reagents. A variety of techniques can be used, including electrolysis and oxidation.
Transformations:
Refining processes vary depending on the desired purity and the type of metal but generally involve the oxidation and reduction of metal impurities. Electrolytic refining may be used after smelting to achieve extremely high purity levels.
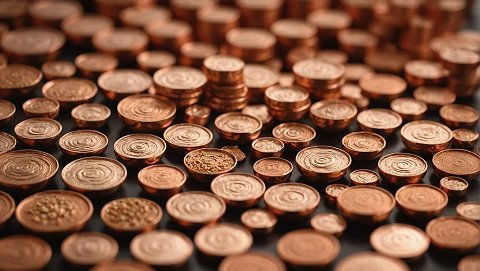
Electrolytic Refining of Copper: In this process, impure copper is made the anode, while pure copper acts as the cathode in an electrolytic cell. The copper ions dissolve from the anode and deposit on the cathode, leaving impurities in solution or forming a sludge.
Thus, the final product is high-purity copper suitable for electrical and industrial applications. Through electrolytic refining, copper can achieve a purity level of 99.99%.
Although a modern method, electrolytic refining has the same aim as alchemical purification of metals, and involves cycles of heating and re-refining.

While alchemy covers many disciplines such as metal work, herbology, medicine, gemology, with a later branch into spirituality, modern metallurgy has specifically developed based on its Neolithic predecessors. In various disciplines, the same processes can have different names.
Non-Fiction Books:
Fiction Books:
READ: Lora Ley Adventures - Germanic Mythology Fiction Series
READ: Reiker For Hire - Victorian Detective Murder Mysteries