Etch Carnelian Beads Like It's Indus Valley 2500 BCE
- Sylvia Rose
- Oct 24, 2024
- 5 min read
The Indus Valley Civilization of the Bronze Age is one of the earliest urban societies, famous for trade, inventiveness and extraordinary artisanship. Among coveted creations are etched carnelian beads, first appearing c. 2500. Here's the secret to the etching process.
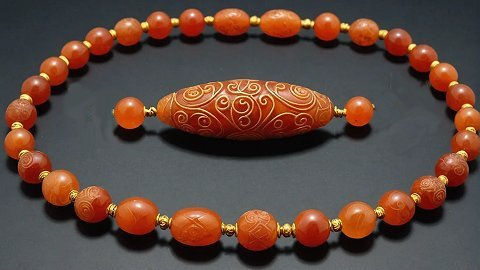
Visually stunning, etched carnelian beads are highly desired along trade routes spanning vast regions. The craft of etching these beads delights artists, archaeologists and historians, revealing remarkable skills and artistic expression.
This is a guide to the intricacies of etching carnelian beads, materials involved and the chemistry behind the process. Get to know unique qualities of carnelian, and how artisans create stunning patterns using materials like soda and plant ash, a secret kept for millennia.
The art of bead-making goes back to prehistory when people collect pretty or otherwise significant stones. The holes are done by hand, a tedious process. They're hand-drilled or made with a process of pecking, or precise hammering with a harder stone.
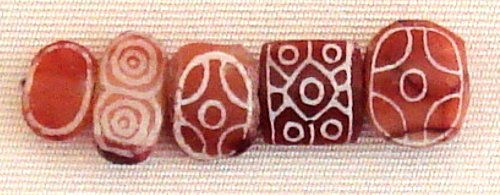
Carnelian is a relatively hard stone, given a 7 on the Mohs scale. It's harder than glass (6) but less than emerald (9) or diamond (10). The Indus Valley Civilization, flourishes from 3300 BCE primarily in the region of Pakistan, part of Afghanistan and North India.
What is Carnelian?
Carnelian is the stone favored by etchers and traders, and no wonder. With a vibrant orange to reddish-brown hue it seems to have an inner glow. Variable color tones can appear in the same rock. Carnelian belongs to the family of chalcedony, a type of silica mineral.
Thus it's a member of the quartz family. Its beautiful color comes from iron oxide, which provides the warm hues. This semi-precious gemstone has been associated with vitality and energy for centuries, often used in jewelry and decorative items.
Highly valued in antiquity, carnelian is favored for rich color and relative ease of workability. It's a good carving stone. The name derives from the Latin “carnis,” meaning "flesh."

For etching, artisans favor the redder stones due to the contrast, while gold-orange toned stones are often used in jewelry and decor. Sumerians and Egyptians also work with the stone, but the Indus Valley artisans most esteemed.
Aside from visual aesthetic qualities, carnelian is given spiritual protective and healing properties, making it a popular choice in jewelry and amulets. In Egypt the stone represents the Sun.
During the time of the Indus Valley Civilization (c. 3300 - 1300 BCE) the stone and beads are sought for bright colors and smooth surfaces, embodying beauty and status. Historical records suggest crafters produce about 300,000 beads over the civilization’s lifespan.

Carnelian is abundant in regions like modern-day Pakistan, India, Afghanistan, and Brazil. Due to its turbulent geological formation Pakistan yields some of the most beautiful stones in the world.
Where Does Ash Get Its Etching Power?
The art of etching carnelian beads relies on soda and plant ash, widely available materials in the Indus Valley. Soda, primarily sodium carbonate, is a powerful alkaline agent. Sodium carbonate is the disodium salt of carbonic acid with alkalinizing property.
Dissolved in water, sodium carbonate forms carbonic acid and sodium hydroxide. Carbonic acid is widely used in the production of soft drinks, artificially carbonated sparkling wines, and other bubbly beverages.
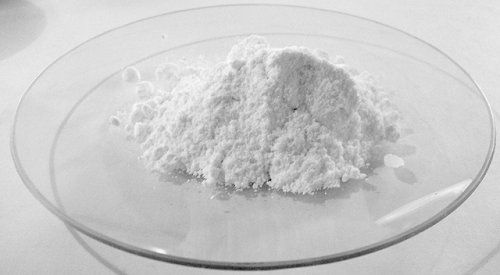
Plant ash, residue of burnt trees and shrubs, also contains silica and other minerals, and is rich in sodium and potassium carbonates. These are created during combustion of organic materials (wood). enhancing its effectiveness as an etching agent.
Potassium, calcium, and magnesium carbonate or oxides are present in comparatively large quantities giving the ashes a strongly alkaline reaction. This can neutralize acid soils and used as a companion to fertilizer.
Wood ash can also pacify the legendary German wicked ash tree woman. In the lab, mixed with water, the compounds of the ashes dissolve to produce a mildly basic solution.
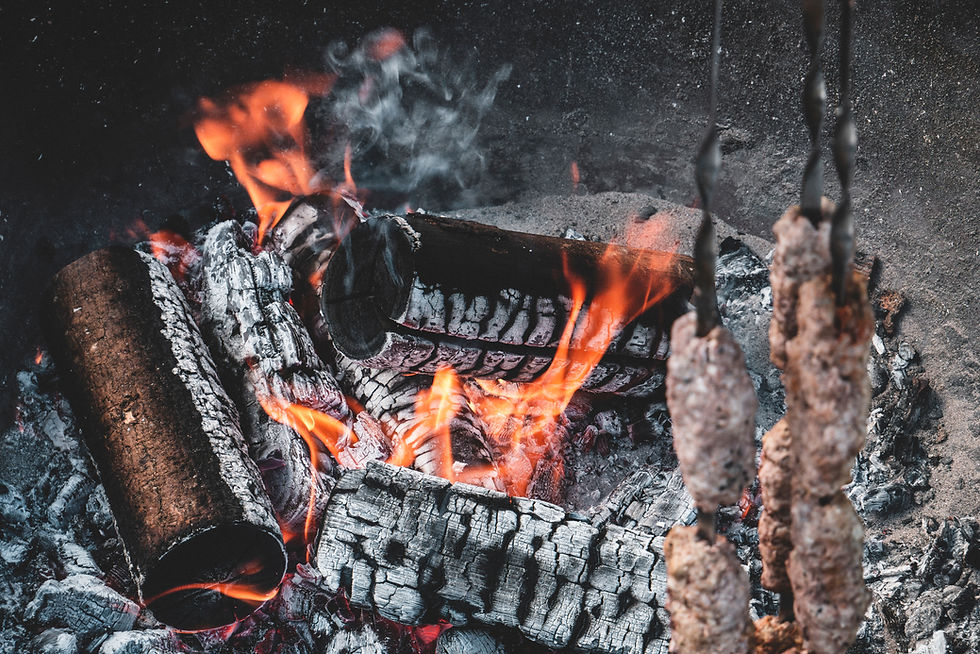
Steps in the Etching Process of the Indus Valley 2500 BCE
Here’s a step-by-step guide to replicating the ancient etching method used by Indus Valley artisans:
Step 1: Material Preparation
Select the Carnelian: The artisan starts with high-quality carnelian, ensuring the stones are free of fractures and imperfections. The ideal size for beads depends on design preference. Even smaller beads are receptive to detailed etching.
Shaping the Beads: Carnelian is shaped into beads using tools made from harder stones or metals. The shaping results in various forms, from simple spheres to complex designs.
Prepare the Ash: Collect ash from burnt wood or plants known to have high alkaline content. Sift ash to remove any larger particles that could damage the beads.

Step 2: Create the Etching Paste
Ancient artisans mix soda or plant ash with water to create a thick etching paste. The consistency of this paste is crucial for effectively penetrating the bead's surface.
Mixing the Paste: In a bowl, combine the ash with a controlled amount of water to form a thicker paste. The consistency should be such that it can easily adhere to the surface of the beads but doesn't run off. Add more ash if it's too runny, more water if too thick.
Step 3: Apply the Paste
Draw, lightly incise or create a stencil of the pattern. Start with basic shapes as there's a learning curve, which also helps the artisan get familiar with the materials.

The prepared paste is rendered onto the surface of the shaped beads. Using a toothpick, metal rod, stick, stiff brush or stippling brush, create the design with the etching paste.
Artisans may shift techniques to achieve different line depths, textures and patterns, ensuring consistency. Some designs are specific to certain makers, whose reputations become known through trade and travel.
Step 4: Curing
Let It Sit: Allow the beads to sit undisturbed for several hours. The alkaline nature of the ash will gradually react with the carnelian's surface, creating the desired white patterns. Length of curing can vary. Alternately, gently heating the beads speeds up the reaction.

Step 5: Rinse and Polish
Rinse Off: Rinse the beads thoroughly in water to remove any residual ash. This step is crucial to reveal the contrasting patterns created by the etching process.
Polish the Beads: Finally, polish the beads using a soft cloth to enhance natural finish and start stringing.
Drilling bead holes in the time of the ancients is a feat of skill and patience. Boring holes into the beads uses rotating flint drills set into wooden handles. Flint is the same hardness as carnelian.
These days carnelian is readily available in bead shops, gem shops and online. As a semi-precious gem carnelian is both beautiful and affordable. Pre-made carnelian beads are easiest to work with unless the artisan wants to stay in c. 2500 BCE and do the hand drill.

Non-Fiction Books:
Fiction Books:
READ: Lora Ley Adventures - Germanic Mythology Fiction Series
READ: Reiker For Hire - Victorian Detective Murder Mysteries